Optimizing Repairs with Durable Replacement Parts
The article emphasizes the importance of using high-quality replacement parts that meet original eq…….
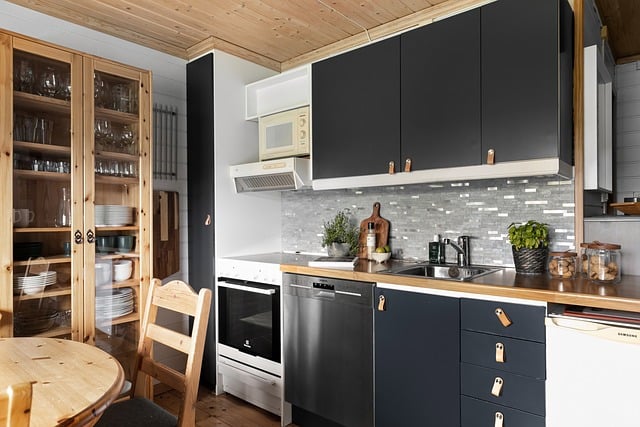
The article emphasizes the importance of using high-quality replacement parts that meet original equipment manufacturer (OEM) standards for long-lasting repairs. These parts are carefully engineered from superior materials, designed to be durable and compatible with existing systems. They undergo extensive testing to ensure they can withstand regular wear and tear and function reliably over time. Choosing these vetted parts not only ensures a repair that lasts but also represents a sustainable investment in maintaining the functionality and longevity of equipment. Quality is paramount, as it affects the part's ability to resist environmental factors and perform well. Precision engineering during manufacturing, robust design, advanced protective technologies like heat treatment or surface coating, and a reputable manufacturer's warranty policies are all critical in ensuring that replacement parts will extend the lifespan of the repaired machinery, electronics, or vehicles. Compatibility with existing systems, adherence to manufacturer guidelines, industry standards, and meticulous installation practices further contribute to sustained performance and cost savings by mitigating the risks associated with inferior components. Regular, proactive maintenance is also crucial for prolonging operational life, requiring scheduled inspections, cleaning, lubrication, and the use of premium replacement parts to enhance durability and system performance.
When it comes to ensuring the longevity of your vehicle or appliance through lasting repairs, the choice of replacement parts is paramount. This article delves into the critical role of quality replacement parts in sustaining peak performance and reliability. We will explore the key factors that determine part durability, emphasizing the importance of compatibility in repair work to ensure optimal functionality. Sourcing top-tier components is a pivotal step in any maintenance endeavor; our guidance will steer you toward reliable suppliers. Moreover, we will outline installation best practices and provide essential maintenance tips aimed at extending the lifespan of your replacement parts. With a comprehensive approach to repair quality, your investment in longevity will be well-founded and enduring.
- Understanding Quality Replacement Parts
- Key Factors Determining Part Durability
- The Role of Compatibility in Repair Work
- Sourcing Top-Tier Replacement Components
- Installation Best Practices for Longevity
- Maintenance Tips to Extend Part Lifespan
Understanding Quality Replacement Parts
When addressing the necessity for quality replacement parts in lasting repairs, it’s crucial to assess the standards and specifications that define a part as ‘quality.’ These parts are meticulously crafted to match or exceed the original equipment manufacturer’s (OEM) specifications, ensuring compatibility with your device or system. The materials used in their construction are of high caliber, often made from the same durable alloys and composites found in genuine components. This commitment to material integrity means that these parts can endure similar wear and tear as the original, offering a reliable and long-lasting solution.
Furthermore, quality replacement parts are subjected to rigorous testing procedures to ensure they meet stringent performance benchmarks. These tests often replicate the conditions they will face in real-world applications, confirming their ability to function effectively over time. By choosing parts that have been through such evaluations, consumers can feel confident that they are investing in solutions that won’t compromise the longevity or functionality of their equipment. This attention to detail and commitment to quality underpins the value proposition of these replacement parts, making them an essential consideration for those seeking repairs that stand the test of time.
Key Factors Determining Part Durability
When selecting quality replacement parts for lasting repairs, understanding the key factors that determine part durability is paramount. High-quality materials are a cornerstone of durable parts; they must withstand environmental stressors and resist wear and tear over time. The manufacturing process also plays a critical role—precision engineering ensures components fit perfectly with minimal friction, which can extend the life of the part. Additionally, the design of the part should be scrutinized for robustness; components that are engineered to be resilient will inherently last longer.
Beyond material and design, the compatibility of replacement parts with existing systems cannot be overstated. Parts must seamlessly integrate with other components to ensure optimal functionality and longevity. Moreover, reputable manufacturers often incorporate advanced technologies such as heat treatment or surface coating to enhance part resilience against corrosion and extreme temperatures. Lastly, the track record of the manufacturer, including their warranty policies and customer feedback, is a reliable indicator of the durability one can expect from their parts. Consistently opting for parts that meet these criteria will contribute significantly to the longevity of the repaired equipment.
The Role of Compatibility in Repair Work
When it comes to repairing machinery, electronics, or vehicles, the compatibility of replacement parts is paramount. A part’s ability to integrate seamlessly with existing systems is crucial for maintaining functionality and performance. Compatibility ensures that new components do not disrupt the operations of other elements within the system, which could lead to malfunctions or reduced efficiency. It involves more than just fitting into a physical space; it encompasses the intricate interplay between different components, including their electrical, mechanical, and sometimes software interactions. Manufacturers design parts with specifications that align with those of the original equipment manufacturer (OEM), which facilitates easier integration. This alignment is not merely about using the same materials or matching dimensions; it also requires a deep understanding of the intended system’s design principles and how each part contributes to its overall performance. By selecting parts that are truly compatible, repair professionals can restore devices to their optimal state, ensuring longevity and reliability. This meticulous approach to part selection is essential for any repair work aiming at not just a temporary fix but lasting repairs that stand the test of time.
Sourcing Top-Tier Replacement Components
When it comes to ensuring the longevity and performance of equipment or vehicles, sourcing top-tier replacement components is a critical aspect of maintenance. High-quality parts are not merely substitutes; they are integral to maintaining the original specifications and operational integrity of the system. Manufacturers design machines with specific tolerances and functionalities in mind, and using replacements that align with these parameters ensures that the repaired item operates as intended after the repair.
The pursuit of quality begins with identifying reputable suppliers who specialize in providing components that meet or exceed the original standards. These suppliers often have established relationships with OEMs (Original Equipment Manufacturers), ensuring that the parts are authentic and compatible. Additionally, they typically undergo rigorous testing and quality control processes to ensure they perform as well as, if not better than, their predecessors. By investing in top-tier components, users can avoid the pitfalls of subpar replacements that might lead to frequent repairs or premature system failure. This investment in quality is a proactive measure that contributes significantly to long-term cost savings and reliable performance.
Installation Best Practices for Longevity
When addressing installation best practices for ensuring the longevity of replacement parts, it is crucial to adhere to manufacturer guidelines and industry standards. Proper preparation of the system or component for the new part is a foundational step; this includes cleaning, inspecting, and priming surfaces as necessary to ensure a secure bond. Selection of the right tools and materials for the installation process is equally important, as they can significantly affect the quality and durability of the repair. Technicians should be well-versed in the specifications of the parts they are installing, including any tolerances or clearance requirements that could impact performance.
Throughout the installation process, care must be taken to maintain clean conditions and avoid contamination, which can lead to premature failure. Precision is key; components should be aligned correctly, and fasteners should be tightened to the specified torque without overloading or stressing the parts. Post-installation, a thorough inspection should be conducted to confirm that everything is functioning as intended. Additionally, documenting each step of the installation process can aid in future maintenance and troubleshooting. By following these best practices, repairs using quality replacement parts are more likely to last longer and maintain optimal performance.
Maintenance Tips to Extend Part Lifespan
Regular maintenance is key to extending the lifespan of replacement parts in any machinery or system. To begin with, adhering to a strict maintenance schedule can prevent minor issues from escalating into major failures. This involves routine checks to ensure all components are functioning as intended. For instance, cleaning and lubricating moving parts can reduce friction and wear, thereby preserving their integrity over time. Additionally, monitoring fluid levels and replacing filters regularly in hydraulic or pneumatic systems is crucial for maintaining optimal performance.
Moreover, using high-quality replacement parts from reputable manufacturers not only ensures compatibility with your equipment but also guarantees that they are designed to last longer. These parts often come with better materials and tighter tolerances, which can withstand more intense use without degrading prematurely. It’s also important to keep detailed records of maintenance activities, which can help in identifying patterns or recurring issues that may signal the need for part upgrades before a failure occurs. By combining quality parts with diligent maintenance practices, you can significantly extend the lifespan of your equipment and minimize costly downtime.
In conclusion, investing in quality replacement parts is a critical step towards ensuring lasting repairs for your systems. By understanding the key factors that determine part durability, prioritizing compatibility during the repair process, and sourcing top-tier components from reliable suppliers, you set the foundation for effective and enduring fixes. Coupled with adhering to best practices in installation and following maintenance tips to extend part lifespan, the result is a robust solution that stands the test of time. Ultimately, this conscientious approach to repair work not only saves costs in the long run but also contributes to reliability and performance, ensuring that your systems operate at their best for years to come.