GE Dryer Maintenance and Repair: Ensuring Consistent Drying Reliability
When servicing a GE dryer, it's essential to refer to the correct service manual for your spec…….
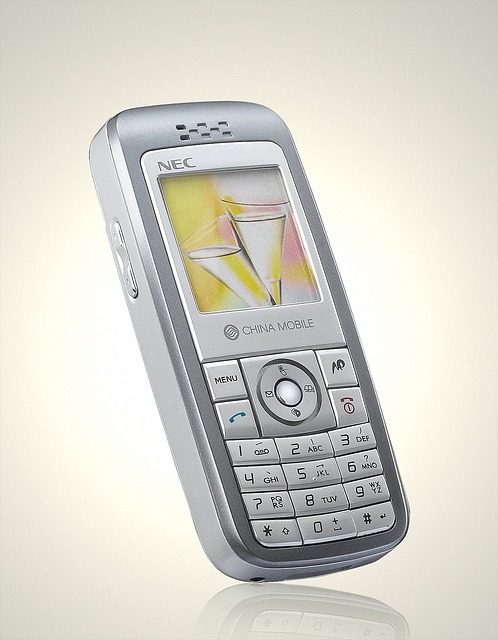
When servicing a GE dryer, it's essential to refer to the correct service manual for your specific model, which offers detailed instructions, wiring diagrams, and parts lists for troubleshooting and repair. These manuals help technicians diagnose and fix issues efficiently, ensuring your dryer operates at its best. GE also provides guides for addressing common problems like starting failures or poor drying. For instance, a lack of heating might be due to a faulty heating element or thermostat, which can be fixed by following the appropriate steps. Regular maintenance, such as cleaning lint filters and inspecting belts and vents, is crucial for preventing malfunctions and extending the dryer's life. In case of persistent issues, consulting professional repair services is advisable. Consistent upkeep, including post-use lint filter cleaning and semi-annual deep cleans, ensures the dryer remains safe and efficient, with optimal performance sustained over time.
When it comes to maintaining the optimal performance of your GE dryer, knowledge is your greatest ally. This article delves into the intricacies of GE dryer repair, ensuring that you can sustain top-notch drying efficiency. We’ll explore your specific dryer model, identify common issues afflicting GE dryers and their remedies, guide you through a systematic approach to troubleshooting, highlight essential components to monitor, and provide tips for regular maintenance to preserve peak performance. With these tools at your disposal, you’ll be equipped to handle any drying challenges that arise, keeping your laundry routine smooth and efficient.
- Understanding Your GE Dryer Model for Effective Repair
- Common Issues and Solutions in GE Dryers
- Step-by-Step Guide to Troubleshooting GE Dryer Problems
- Essential Components to Check Before Calling a Technician
- Maintaining Peak Performance: Tips for Regular Upkeep of Your GE Dryer
Understanding Your GE Dryer Model for Effective Repair
When addressing repairs on your GE dryer, the first step is to familiarize yourself with the specific model you own. Each GE dryer model may have unique components and design features that affect how repairs are performed. By identifying your model number, often found on a label inside the dryer’s door or on the rear panel, you can access detailed service manuals provided by GE. These manuals are invaluable resources, offering precise instructions, wiring diagrams, and parts lists tailored to your particular unit. This information enables technicians to pinpoint the exact issue and perform effective repairs, ensuring that your dryer operates reliably and efficiently.
In addition to the service manual, GE provides troubleshooting guides that help you diagnose common problems such as failure to start, excessive noise, or insufficient drying performance. These guides outline potential causes for each problem and suggest appropriate repair actions. For instance, if your dryer isn’t heating up, the issue might be with the heating element or the thermostat. By understanding these potential issues and following the correct repair procedures, you can effectively address the malfunction, restore your dryer to full functionality, and maintain its performance over time.
Common Issues and Solutions in GE Dryers
GE dryers, like any other appliance, can encounter various issues over time. One prevalent problem is clogged lint filters, which can reduce airflow and drying efficiency. To address this, it’s advisable to clean the lint filter after every use or at least once a month. This simple maintenance step can prevent longer-term issues such as overheating and excessive drying times. Another common issue is the dryer not starting, which could be due to a tripped circuit breaker or a faulty electronic control board. In such cases, checking the power source and resetting the breaker or replacing the board, if damaged, can restore functionality.
Furthermore, if the GE dryer is not heating, potential causes include a malfunctioning heating element, a defective thermostat, or a broken thermal fuse. Troubleshooting involves inspecting these components and replacing them as necessary. It’s important to follow safety precautions and disconnect the dryer from power before attempting any repairs. If the drum isn’t rotating, the issue might lie with the drive belt, which could be stretched or broken. Replacing the belt will typically resolve this problem. Additionally, excessive noise during operation may indicate that the rollers or glides have worn out and require replacement to ensure smooth operation and prolong the appliance’s lifespan. Regularly inspecting these parts can help prevent unexpected failures and maintain reliable drying performance.
Step-by-Step Guide to Troubleshooting GE Dryer Problems
When encountering issues with your GE dryer, a systematic approach to troubleshooting can help you identify and resolve the problem efficiently. If the dryer isn’t heating, begin by verifying that the power is connected and the circuit breaker has not tripped. Ensure the dryer’s selected settings are appropriate for the load size and that the lint filter is clean, as a clogged filter can impede airflow and cause overheating. If the drum isn’t rotating, inspect the drive belt to check for signs of wear or damage; if worn, it should be replaced. The drums may also bind due to excessive lint accumulation, which requires careful removal of the lint and potentially retightening the drum rollers.
For problems related to the dryer not starting, first, listen for a click when pressing the start button; this indicates power is reaching the control board. If there’s no click, check the electrical connections for looseness or disconnection. If the dryer starts but stops abruptly, the thermal fuse might have blown due to overheating, which would necessitate replacement. Additionally, a continuous running dryer may indicate a malfunctioning door latch or switch; inspect these components for proper function. Always adhere to safety precautions and consider unplugging the dryer before beginning any repairs to prevent electric shock. If troubleshooting steps do not resolve the issue, it is advisable to contact a professional technician for further assistance.
Essential Components to Check Before Calling a Technician
When your GE dryer isn’t functioning as it should, a preliminary inspection can often pinpoint the issue before involving a technician. A key step in this process is identifying the essential components that are commonly responsible for malfunctions. The first component to check is the heating element, which is crucial for drying clothes. If the dryer isn’t heating at all or is taking an unusually long time to do so, the element may be faulty and require replacement. Additionally, verify the performance of the temperature sensor and the thermal fuse. These components work in tandem to ensure the dryer reaches the correct temperature safely. A malfunctioning sensor can lead to improper heating, while a blown thermal fuse will prevent the dryer from turning on for safety reasons. Ensure that the exhaust duct is clear of blockages as well. Obstructions can restrict airflow, causing the dryer to overheat or fail to operate effectively. Lastly, inspect the drum bearings and glides. If the drum won’t turn or makes unusual noises during operation, these components might need maintenance or replacement to restore optimal performance. By checking these critical parts, you can often resolve common issues without professional assistance, saving time and money. However, if after your inspection the dryer still isn’t functioning correctly, it’s advisable to call a technician for further diagnosis and repair.
Maintaining Peak Performance: Tips for Regular Upkeep of Your GE Dryer
Regular maintenance is key to maintaining the peak performance of your GE dryer. To ensure optimal drying efficiency, it’s important to clean the lint filter after each use and thoroughly inspect and clean the entire lint screen at least every six months. Lint buildup not only reduces airflow but also poses a fire hazard. Additionally, check the exterior vent for blockages periodically, as a clogged vent can impede proper exhaust and reduce drying effectiveness. Use a flexible vent brush to clear any obstructions.
For long-term reliability, monitor the dryer’s drum and belt regularly. A worn or damaged drum could affect the dryer’s ability to tumble clothes properly. If you notice excessive noise or vibration, inspect the drum and belt for signs of wear; replace them if necessary. Also, keep an eye on the gas line and igniter in a gas dryer, ensuring they are clean and functioning correctly. Regularly scheduled maintenance will not only extend the lifespan of your GE dryer but also ensure that it operates safely and efficiently, delivering reliably dried clothes every time.
ensuring the longevity and efficiency of your appliance. Regular maintenance, understanding your model’s specific needs, and being prepared to tackle common issues can keep your GE dryer operating at peak performance. By following the troubleshooting steps outlined in this article, you empower yourself to handle a variety of problems, potentially saving time and money. Remember to inspect essential components and perform routine upkeep as detailed; these proactive measures will help maintain the reliability of your drying performance. With these insights, your GE dryer can continue to serve as a dependable ally in your daily routines.